Edmund Sides is a highly experienced and accredited Geologist who authors Digbee Reports and has written this article about the basics of Rare Earth Elements (REEs).
What are Rare Earth Elements?
The rare earth lanthanides comprise the 15 elements with atomic numbers from 57 to 71 (Lanthanum (La), Cerium (Ce), Praseodymium (Pr), Neodymium (Nd), Samarium (Sm), Europium (Eu), Gadolinium (Gd), Terbium (Tb), Dysprosium (Dy), Holmium (Ho), Erbium (Er), Thulium (Tm), Ytterbium (Yb), and Lutetium (Lu)). Rare earth elements (REEs), as referred to in this report, include the 14 naturally occurring lanthanides plus yttrium, as illustrated in Figure 1. Promethium (Pm), with atomic number 61, is not shown as it does not occur naturally.
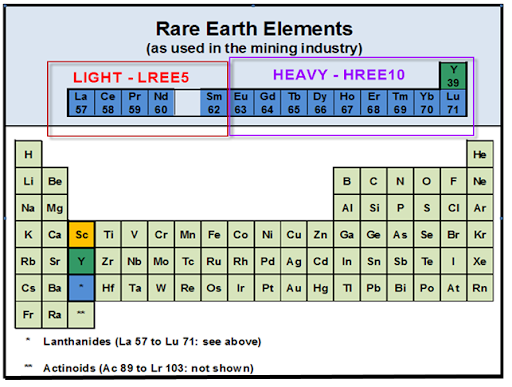
Reports on REE projects frequently divide the REEs into light (LREE) and heavy REE (HREE) groups, as illustrated in Figure 1. This division reflects the fact that:
- The LREEs are naturally more abundant and consequently tend to be lower in value than the HREEs which tend to be scarcer and more valuable.
- During hydrometallurgical processing of REE concentrates, the LREE and HREE groups of elements tend to be separated out together during different parts of the process.
The terms LREE5 and HREE10 shown in Figure 1 are used by the author to indicate the
number of elements have been grouped together for these categories, since some workers
use slightly different groupings. For instance, some authors assign the elements samarium, gadolinium and europium to a separate intermediate group referred to as the medium rare earth element (MREE) group.
REE assay grades and prices are generally based on the rare earth oxide (REO) compounds. Where assays are reported as REE grades, they are converted to the corresponding REO grade by multiplying by a constant factor based on the atomic weights of the elements making up each particular REO.
When considering the term rare earth element it should be appreciated that the adjective rare means “strange” rather than “scarce”. In fact, all of the naturally occurring REEs are more abundant in the earth’s crust than gold and cerium is more abundant than copper.
What are rare earth elements used for?
The individual qualities of the different REEs mean that they are used in a large number of specialist applications, ranging from lighting and optics to electronic displays to permanent magnets and missile guidance systems, as summarised in Figure 2.
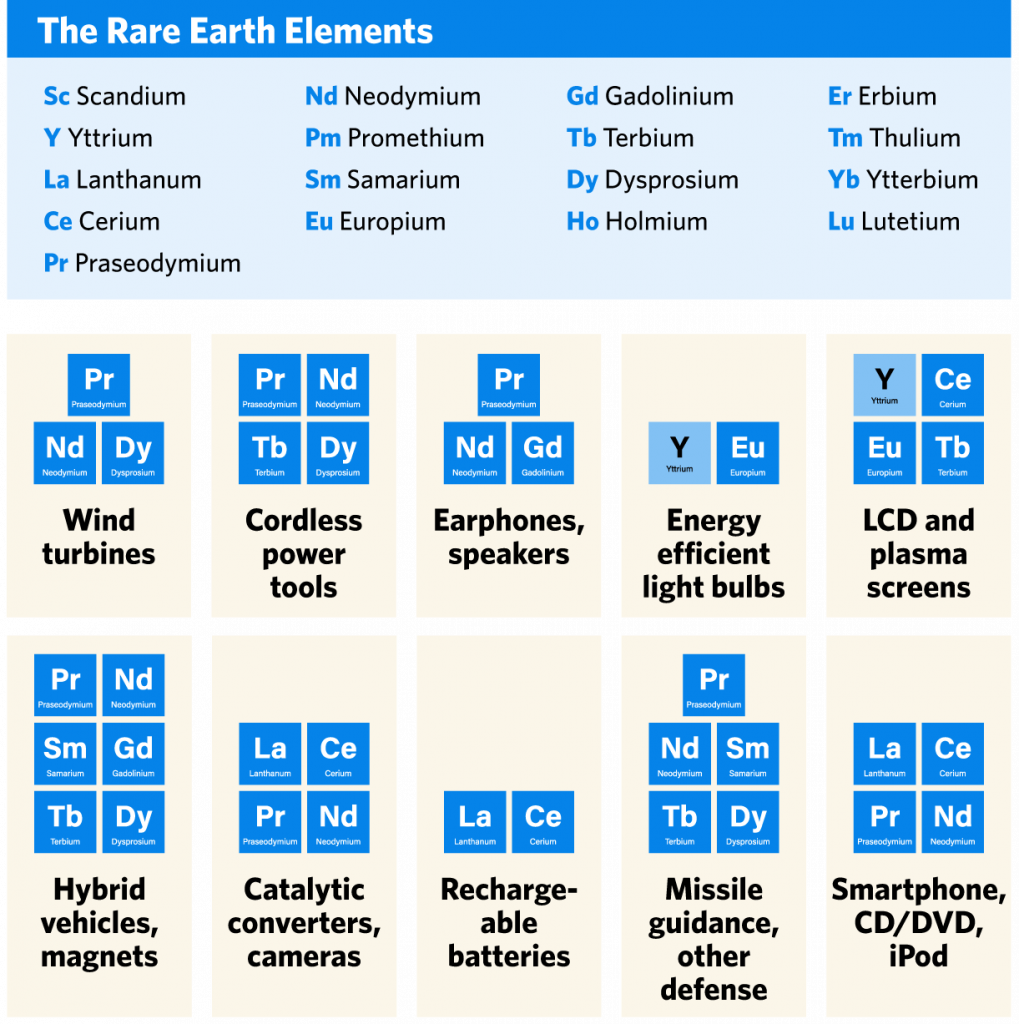
Demand for rare earth elements in several of these applications is forecast to increase in future years, for example rechargeable batteries used in electric cars, permanent magnets for use in electric motors in hybrid and electric motor vehicles and wind turbines, and powerful magnets for use in small electronic devices such as computer hard drives. The wide range of applications in which REEs are used, and the lack of suitable substitutes, means that global demand for REEs is likely to continue to grow over the coming years. Where substitutes are available, they are generally are less effective (USGS, 2020).
In terms of value, the most important market for REEs in recent years is in the manufacture of permanent magnets, as illustrated in Figure 3. Such magnets are required for use in the motors and generators of electric and hybrid vehicles, wind turbines, and a variety of other clean energy applications and demand is expected to continue to grow.
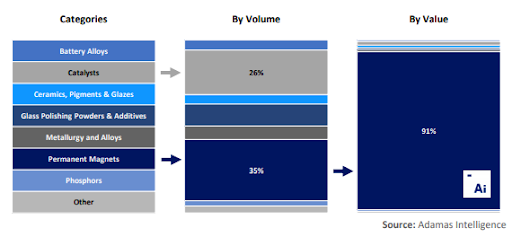
REE magnets have ten times the magnet strength for the same weight as conventional magnets, and there is currently no known substitute. In terms of the manufacture of permanent magnets, the most important REEs are neodymium, praseodymium, dysprosium and terbium. Adamas (2019) forecasts that by 2030, annual demand for neodymium oxide and dysprosium oxide will significantly exceed existing supply leading to depletion of stockpiles and shortages for these metals unless new sources of supply are developed.
Supply
In recent years the mining, processing and production of rare earth oxides has been dominated by China, as illustrated in Figure 4. Prior to 1965, most production of REEs came from monazite in heavy mineral placer deposits. Subsequently, between 1965 and 1985 over half the world’s production came from the Mountain Pass deposit in California, USA.
Since then, China has become the dominant producer of a greatly increased global production of REEs. This is a result of a strategic decision made by China in the early 1990s to become a dominant player in the REE sector, given the importance of REEs in many applications.
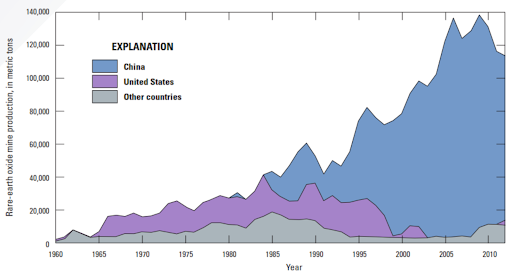
Over the past two decades, China has encouraged the development of industries based on the use of REEs and is reported to have concerns about the depletion of the country’s own REE resources. Export quotas and export tariffs have historically been applied to REE production in order to encourage and protect the development of the industry within China. These policies have resulted in China’s dominance of rare earth resource production, refining, material science, metallurgy, intellectual property, research and development, and commercial and defence applications.
Historically, there have been concerns about the security of supply among users of REEs outside China, and over the past decade China has used restrictions on REE imports as a weapon in trade disputes. Recognising their reliance on China for the supply of rare earth elements, in recent years both the USA and the European Union have included rare earth elements in their lists of critical raw materials.
An important aspect of the supply of REEs is the concentration of production in a limited number of locations and individual mines. Inner Mongolia accounts for nearly 70% of China’s LREE production, with a single mine — the Bayan Obo Mine in the Inner Mongolia region — producing more than 50% of all Chinese rare earth elements. Southern China, where HREEs were first discovered in the 1960s, accounts for most of the country’s HREE production (Stratfor, 2019). The most important current producers of REEs outside of China are the Mount Weld mine in Australia and the historically important Mountain Pass mine in the USA (which was reopened at the end of 2017). Myanmar is reported to be a significant producer but little information is available about its mines and deposits.
Another important consideration in terms of the supply of rare earths is what is referred to as the balance problem. Because groups of individual rare earths occur together in the same minerals they are extracted together in the first stage of production as mineral concentrates. Subsequent processing of the mineral concentrates to separate the individual rare earth elements can then lead to oversupply of some of the more common low value REEs such as cerium when extracting higher value REEs such as neodymium. Adamas (2019) refers to this effect as sacrificial overproduction and predicts that unless other uses are found for elements such as cerium and lanthanum which are in oversupply, then the prices of high-demand elements, such as neodymium, praseodymium, dysprosium and terbium will rise in order to pay for the losses that producers have to incur by necessarily over-producing the other unsaleable, surplus rare earths. The balance problem would also be an important consideration in determining the value of a REE mineral concentrate, depending on the relative proportions of individual REEs contained in it and their amenability to extraction.
Reserves
REEs are not that scarce, being much more common in the earth’s crust than elements such as platinum and gold. Substantial reserves of REEs have been identified in many countries, as illustrated in Table 1, which is based on estimates published by the United States Geological Survey (USGS, 2020).
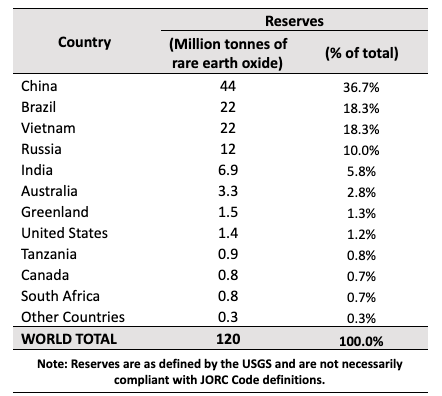
Rare earth element prices
Prices for REEs are mostly quoted for the oxides and metals rather than the mineral concentrates which form the initial product from an REE mine. The metallurgical processing required to produce individual or mixed rare earth oxide products is generally a complex and costly process that has to be tailored to the specific ore and gangue mineralogy of individual deposits. This means that sales of REE mineral concentrates are likely to obtain a much lower price than the value of the equivalent oxide or metal content of the concentrate.
As illustrated in Figure 5, REE prices peaked in 2011 amid concerns over scarcity of supply due to Chinese restrictions on exports. In early 2012 REE prices crashed when there was a reassessment of the effect of the export ban imposed by China in 2010. With the exception of an increase in the prices of praseodymium oxide from the second half of 2013 to early 2015, prices then remained relatively flat until a recent peak in 2017.
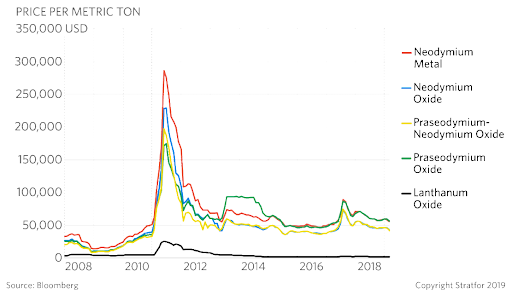
Given the specialist nature of the REE market, new producers are likely to have to rely on off-take agreements with users who wish to ensure security of supply for the sales of some of their products. Increasing concerns about security of supply, in North America and Europe, are stimulating interest in developing their own local REE processing facilities which may provide opportunities for new producers outside of China.
REE processing
The production of rare earth elements is somewhat more complicated than for most precious and base metals. Four main steps are involved in the extraction of REE metals from mineralised rock, as illustrated schematically in Figure 6. A useful overview of some of the processing steps involved is provided in Liyananadirah et al, 2017.
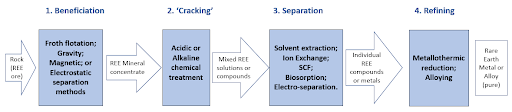
About the author
Edmund Sides is a Geologist with over 30 years experience in the mining industry. He is a Professional Member of the Institute of Geologists of Ireland with Professional Geologist (PGeo) and European Geologist (EurGeol) accreditations. He has worked on a variety of deposit types and commodities, including base metals, gold, iron ore and rare earth elements. His specialities include geological interpretation and modelling; geostatistics; resource estimation; technical reporting; due diligence reviews; and, risk assessment. Edmund has worked on several rare earth element deposits over the past decade. Edmund acted as Competent Person for mineral resource estimates on the Çanakli deposit in Turkey and the Wigu Hill deposit in Tanzania, both of which are development stage REE projects.
Edmund has written Digbee Reports on Marathon Gold Corp’s Valentine Gold project and Pensana Metal’s Longonjo project in Angola. Both are available to buy from https://thedigbee.com/reports
Bibliography
Documents referred to by Edmund Sides when preparing this article include the following:
- Adamas, 2019. Rare Earth Elements – Market Issues and Outlook, Adamas Intelligence, Q2 2019, available from: http://www.adamasintel.com/wp-content/uploads/2019/07/Adamas-Intelligence-Rare-Earths-Market-Issues-and-Outlook-Q2-2019.pdf
- JORC, 2012. The JORC Code, 2012 edition. Australasian Code for Reporting of Exploration Results, Mineral Resources and Ore Reserves. Available from: http://www.jorc.org/docs/JORC_code_2012.pdf
- Liyananadirah et al, 2017. A Review of Rare Earth Mineral Processing Technology by Liyananadirah Mat Suli, Wan Hanisah Wan Ibrahim, Badhrulhisham Abdul Aziz, Mohd Rizauddin Deraman and Nurul Ain Ismail, Chemical Engineering Research Bulletin 19(2017) 20-35. Accessed on 8 July 2020 from: https://www.researchgate.net/publication/319620369_A_Review_of_Rare_Earth_Mineral_Processing_Technology
- Stratfor, 2019. The Geopolitics of Rare Earth Elements. Online article dated April 8, 2019. Accessed 7 July 2020 from: https://worldview.stratfor.com/article/geopolitics-rare-earth-elements
- USGS, 2019a. Rare Earth Element Mineral Deposits in the United States, Circular 1454, Version 1.1, April 2019. Available from: https://pubs.usgs.gov/circ/1454/circ1454.pdf
- USGS, 2019b. Rare Earth Elements – Mineral Commodities Summary, published by the United States Geological Survey. Available from: https://www.usgs.gov/centers/nmic/mineral-commodity-summaries
- USGS, 2020. Rare Earth Elements – Mineral Commodities Summary, published by the United States Geological Survey. Available from: https://www.usgs.gov/centers/nmic/mineral-commodity-summaries